DMP Factory 500 Solution
PERFORMANCE FOR YOUR APPLICATION NEEDS
Derived from 3D Systems’ proven metal additive manufacturing technology, the DMP Factory 500 Solution is engineered and validated for uniform, repeatable part quality, and high productivity in metal 3D printing.
Modularity for a Scalable Factory Solution
The DMP Factory 500 Solution is comprised of function-specific modules designed to maximize efficiency by optimizing utilization. Each module within the factory solution is fully integrated with a Removable Print Module (RPM) which is vacuum sealable for a controlled print environment and engineered to move between printer and powder modules for continuous production workflow.
Printer modules (PTM) are designed for ongoing, 24/7 printing of parts. The Depowdering Module (DPM) and Powder Recycling Module (PRM) are designed to efficiently depowder parts on build platforms and automatically recycle unused powder materials to prepare the RPM for the next build.
Configure your factory setup with the optimum number and type of modules you need to meet your production workflow needs.
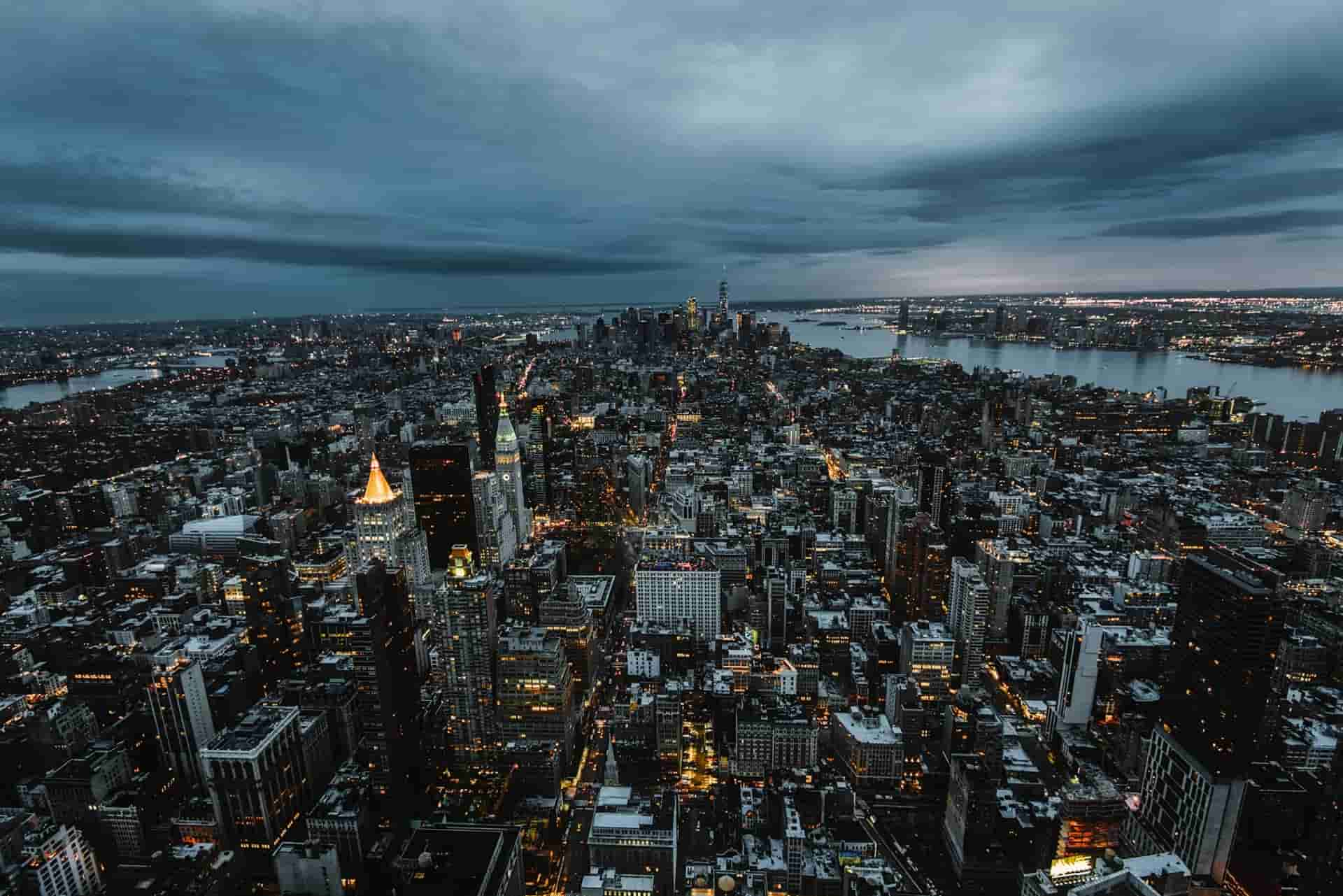
Seamless Large Parts
The intelligent laser configuration and 3DXpert software-driven scan technology of the DMP Factory 500 Solution enable the production of seamless large parts the size of the full build volume (500mm x 500mm x 500mm). This results in the highest surface quality for metal 3D printed parts with outstanding material properties.
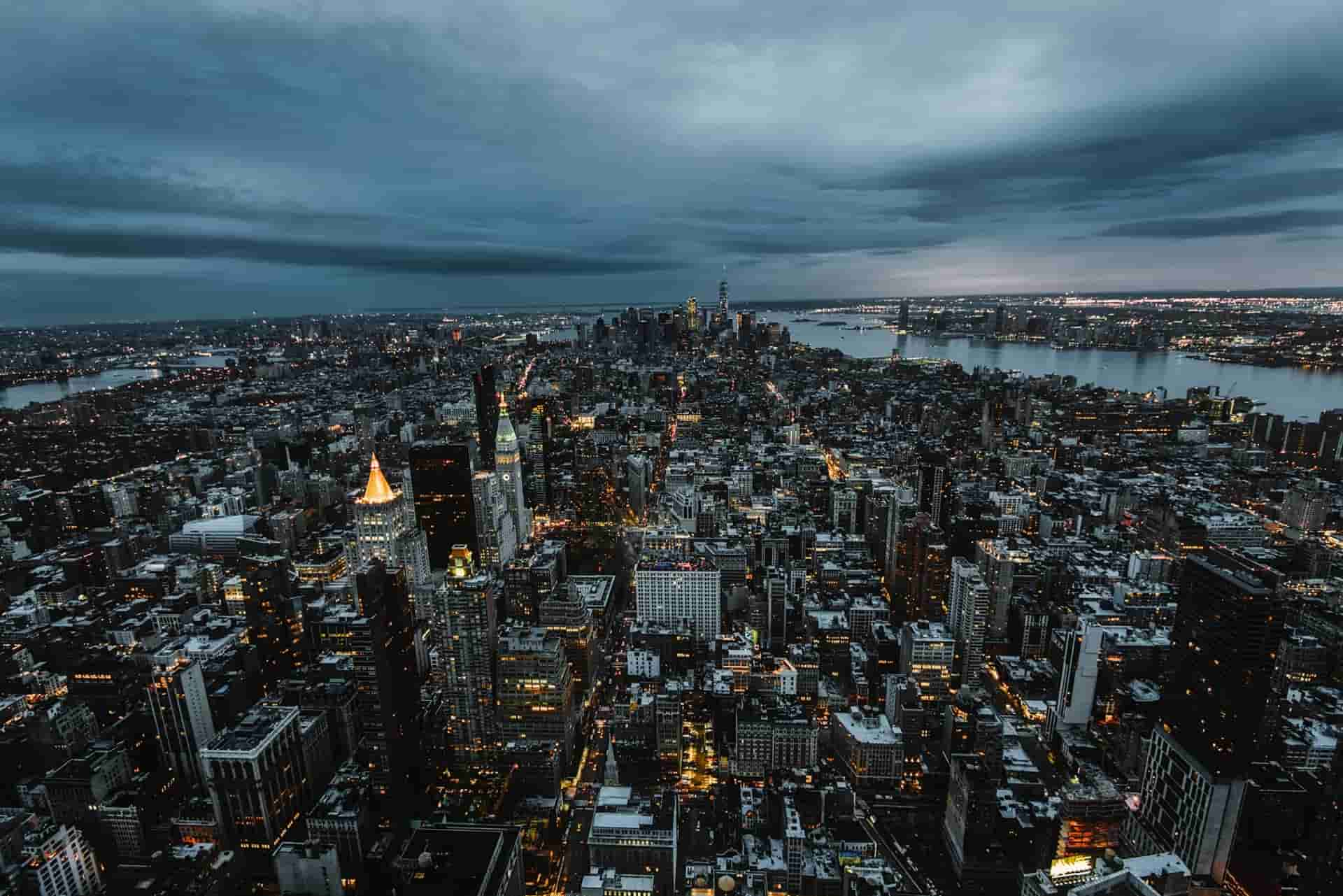
Seamless Large Parts
The intelligent laser configuration and 3DXpert software-driven scan technology of the DMP Factory 500 Solution enable the production of seamless large parts the size of the full build volume (500mm x 500mm x 500mm). This results in the highest surface quality for metal 3D printed parts with outstanding material properties.
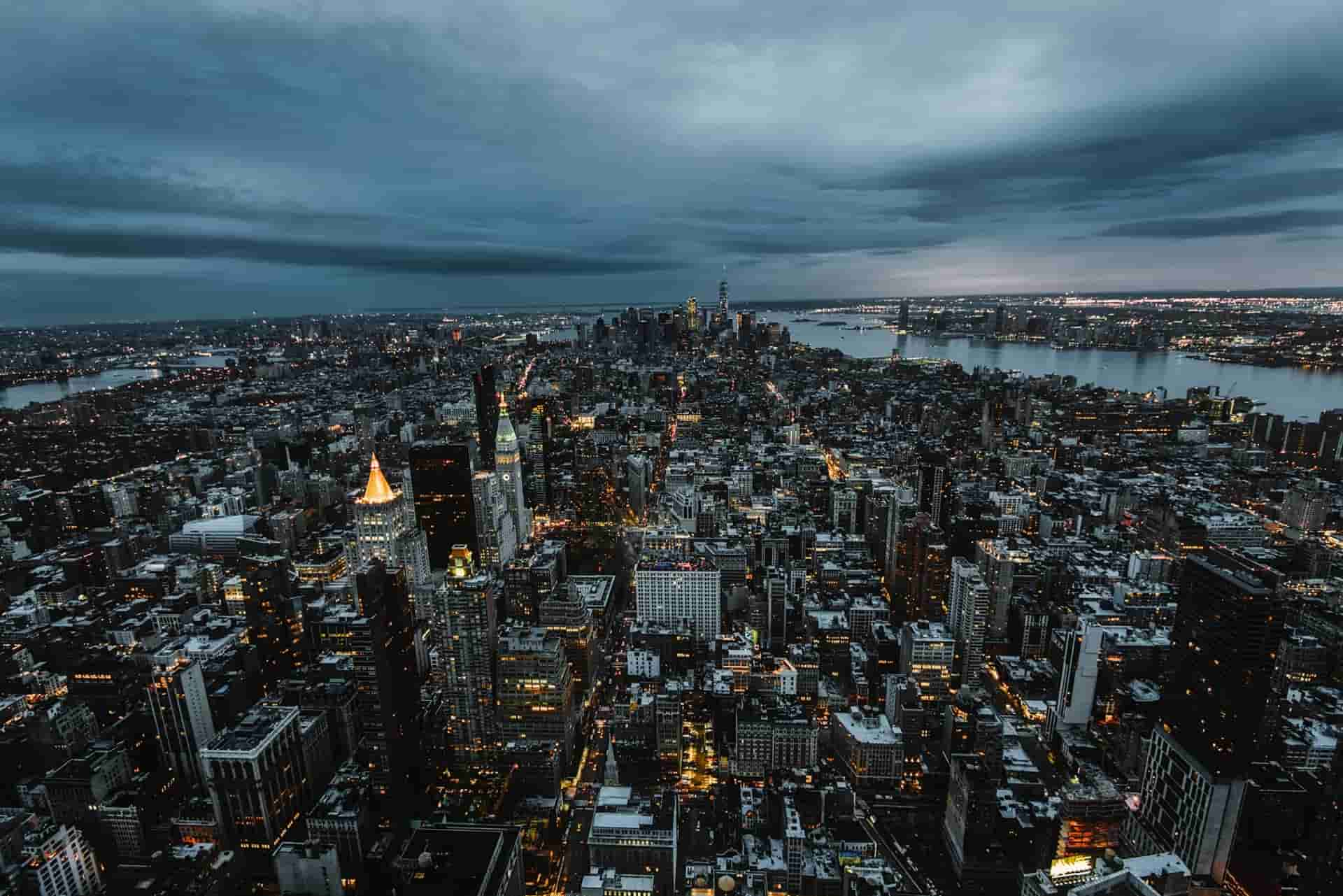
Seamless Large Parts
The intelligent laser configuration and 3DXpert software-driven scan technology of the DMP Factory 500 Solution enable the production of seamless large parts the size of the full build volume (500mm x 500mm x 500mm). This results in the highest surface quality for metal 3D printed parts with outstanding material properties.
Direct Metal Printing Design Guide
An additive manufacturing technique that produces parts in a broad variety of metal alloys
Proven Metal AM Technology
High throughput, highly repeatable metal AM system that generates precision quality parts from a broad range of alloys with high quality material management for maximum powder usage. For companies scaling their metal AM production and requiring limited operator exposure to powder.
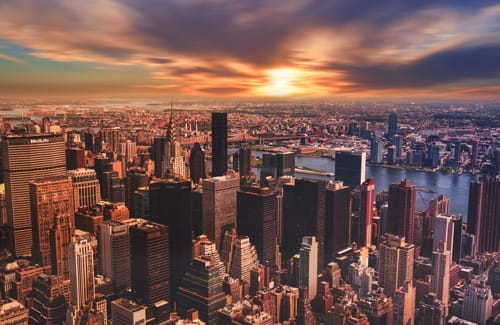
About this printer
- Reduced weight/light-weight design
- Simplified assemblies
- Part count reduction
- Conformal cooling
- Enhanced fluid flow
- Conformal latticework
- Topology optimization
- Mass customization
- Modularity for a scalable factory solution
- Repeatable quality, uniform across the build area
- Metal 3D Printing with lower part costs
- High productivity
- Seamless large parts
- Uses Direct Metal Printing (DMP) technology
- Build volume (W x D x H): 500 x 500 x 500 mm(20.7 x 20.7 x 20.7 in) – height inclusive of build plate
- Unique vacuum chamber concept (O2< 25ppm)
- Quick-swap removable print modules
- Fast bi-directional powder deposition
Commonly Used Materials for the DMP Factory 500
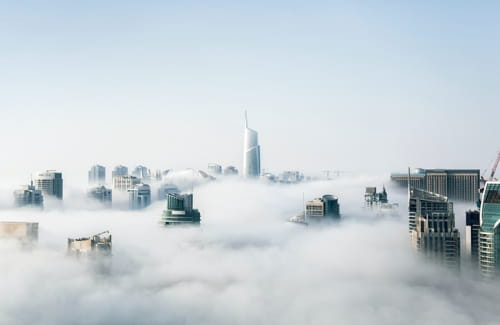
Figure 4 Production
Industry’s first customizable, fully-integrated factory solution for direct digital production
Highlights:
Produce 1 million+ parts per year in a broad range of industrial, dental and custom materials
Customizable and automated direct 3D production solution with configurable, in-line production cells
Direct digital production alternative to traditional manufacturing
Software:
3D Sprint
Find a Broad Choice in Metal Alloys Materials
Advantages of Plastic 3D Printing
3D print with plastics to build almost anything – used for prototyping, manufacturing, anatomical models and more. Select a plastic material and 3D technology to deliver the characteristics you need.
What Can You 3D Print with Plastics?
3D printing with plastics offers many choices for engineering grade materials, elastomers and composites. Do you need flexibility? Strength? Bio-compatibility? More?
What Can You 3D Print with Plastics?
3D printing with plastics offers many choices for engineering grade materials, elastomers and composites. Do you need flexibility? Strength? Bio-compatibility? More?
Advantages of Plastic 3D Printing
3D print with plastics to build almost anything – used for prototyping, manufacturing, anatomical models and more. Select a plastic material and 3D technology to deliver the characteristics you need.