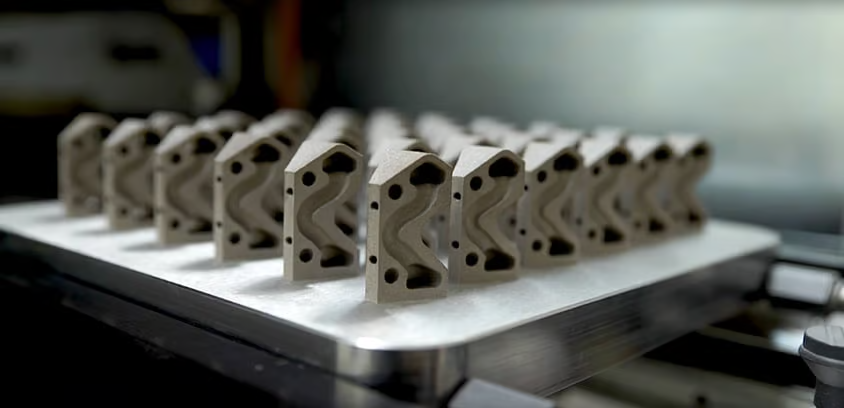
The driving factor behind the surging use of metal 3D printed molds is entirely different from the benefits of plastic 3D printed molds. In fact, metal 3d printed molds can, in certain circumstances, be more expensive and take as long to make as traditional metal molds, but they have one significant advantage: conformal channels.
This feature, that’s only available with 3D printed molds, is igniting a revolution of sorts in the mold-making industry.
Cooling channels are essential in metal injection-molding tools so that parts can be cooled faster and uniformly. The cooling stage represents 70% – 80% of the entire cycle time, so reducing that time over the lifetime of a mold results in significant savings for manufacturers. Proper cooling also affects the dimensional accuracy, surface quality, and mechanical properties of the final product.
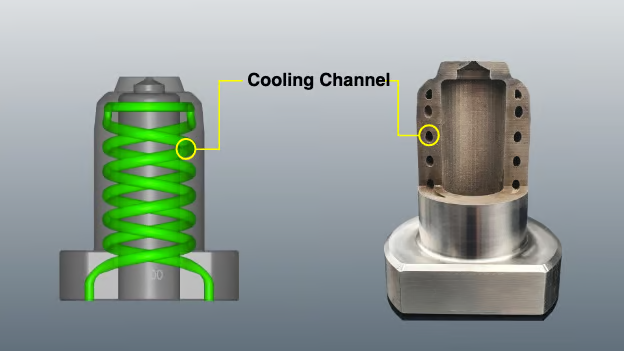
Using conventional machining technologies, cooling channels are added to the mold by drilling in straight lines. The more complex a component’s geometry, the more difficult it is to maintain precise cooling along the contour of the mold. This can make the conventional production of sophisticated components extraordinarily laborious and costly.
Compared to traditional processes, additive manufacturing can create curved cooling channels within a mold shaped to conform to the part’s geometry and provide cooling where it is needed most to improve part quality and reduce cooling times as much as 70%.
Conformal cooling channels are added at the mold design step in CAD software, which can simulate and predict the ideal placement of channels. This design phase, however, adds time and cost to a new metal mold.
Although usually a faster process, metal 3D printing isn’t always. Depending on the complexity of the mold or tool, it can take several days or weeks to produce a final mold. The benefits of metal 3D printed tooling are typically realized in part production, not in the building of the tool itself.
Pros | Cons |
Equal quality to machined molds | Can take longer and cost more than machining |
Opportunity to include conformal cooling channels | Upfront design time and skills required |
It can be a faster method than machining molds | May still require machining |
Uses less raw material than machined molds | Some limited to mold size |
It an be an in-house solution to protect IP | |
Several mold versions can be printed at once | |
Wide selection of out-source manufacturers | |
Parts from metal 3D printed molds have equal quality to parts from machined molds |