From automotive spare parts to satellite antennas, applications for 3D printed aluminum parts are expanding due to an uptick in the adoption of new aluminum materials developed specifically for additive manufacturing and 3D printers that are more finely tuned to optimize these new aluminum alloys. The resulting parts have better material properties than conventionally manufactured aluminum and feature complex geometries only possible with additive manufacturing.
Advantages of 3D Printing Aluminum
Aluminum alloys feature good chemical resistance, are very lightweight, and feature one of the best strength-to-weight ratios of any metal. Combined with silicon and magnesium, it’s the choice of many in the aerospace and automotive industry for its ability to withstand harsh conditions.
One of the biggest advantages of 3D printing in aluminum, or any metal for that matter, is that you can create parts with internal channels and features that aren’t possible to manufacture any other way. You can print a multi-part assembly as one unit, drastically cutting down on manufacturing and assembly time, and developing a more efficient part overall.
3D printing also does not create much waste. By contrast, CNC machining is subtractive. When you’re working with expensive raw materials, anything you can do to minimize waste is a big plus. This is particularly interesting for the aerospace industry, which constantly strives to improve its “buy-to-fly” ratio, the weight of purchased raw material compared to final part weight.
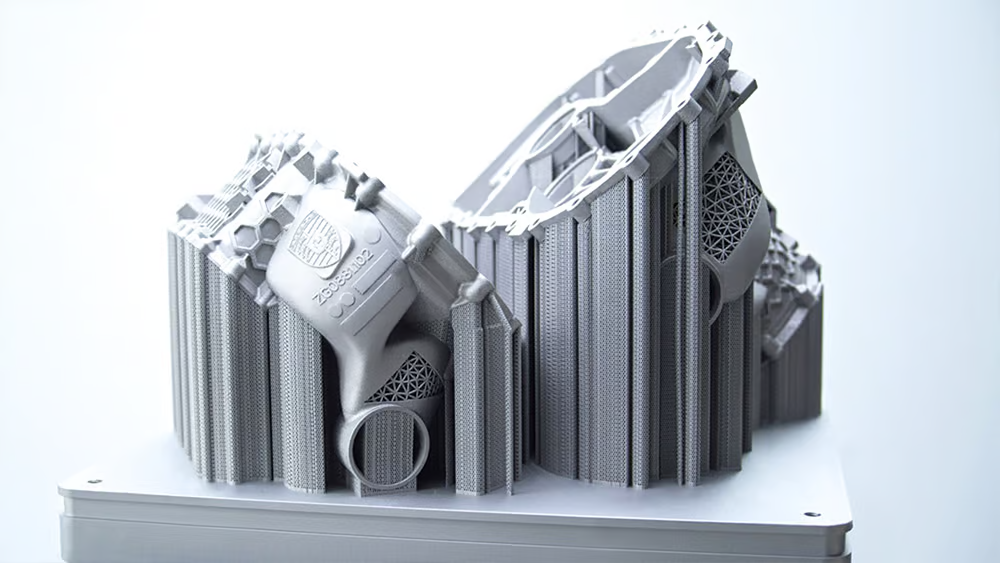
Casting or machining aluminum often has higher production costs and uses more energy during fabrication. There’s also the additional cost of acquiring tooling or molding. Compare that to AM production, using aluminum which can craft highly-precise complex geometries and shapes that would be impossible with any other manufacturing method.
Design work is done with software and manufacturing can be completed without creating physical tools or molds. Additive manufacturers can produce low-volume and custom parts quickly and affordably and emerging technology continues to make both larger production runs and lower operational costs a reality.
How to 3D Print Aluminum
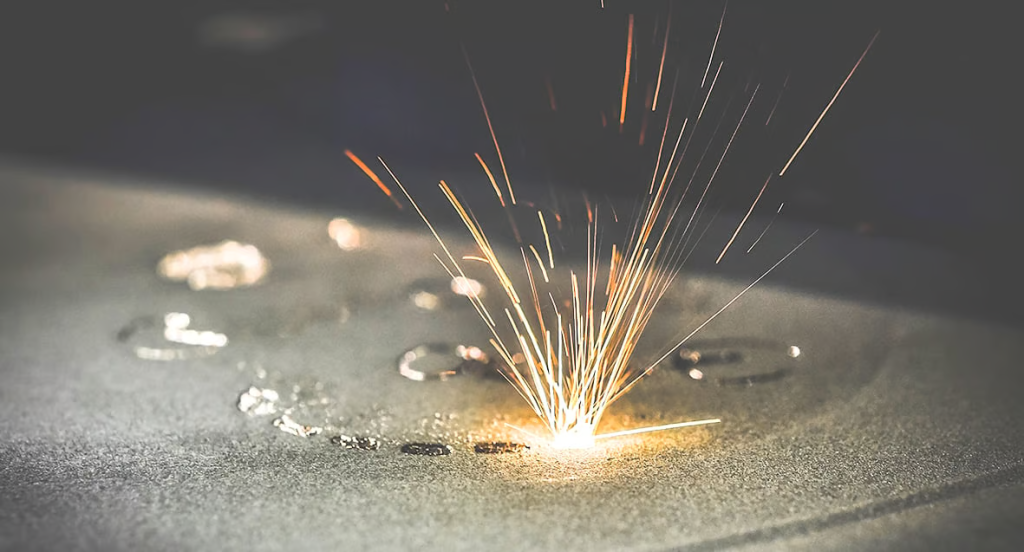
Selective Laser Melting(SLM) is the most common aluminum 3D printing technology, but not every printer with this technology can handle aluminum. Based on the properties of the aluminum-based alloy to be processed, the SLM printing parameters must be optimized and tuned to control porosity, microstructure, and final material properties.
Know Your Aluminum Materials
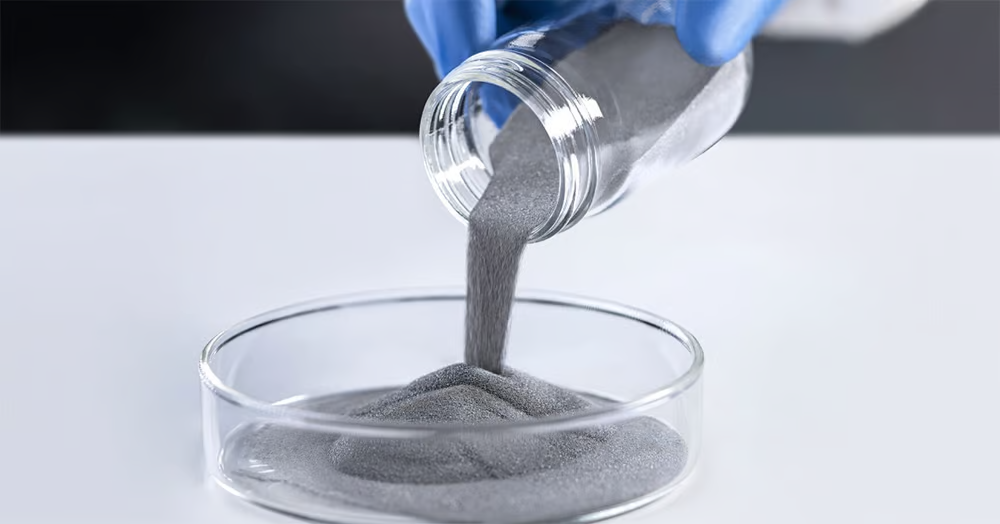
Many of the current aluminum alloys for 3D printing are simple casting alloys, such as AlSi10Mg. These aluminum alloys are not particularly strong, nor can they manage high temperatures. Still, their mechanical properties are suitable for a wide range of applications and the material is “weldable” and, therefore, can be used in 3D printing without cracking. The properties of these materials may be all some companies are looking for in metal 3D printing, but others, especially aerospace and advanced manufacturing, need more.
While there are several different types of aluminum alloys on the market, here are some of the more common ones being used in AM.
- AISi10Mg is the most common aluminum alloy and features solid strength, hardness, and dynamic properties. Its light weight also supports good thermal properties and has strong buildability for use in challenging geometries. Uses include housings, ductwork, engine parts, and production tools.
- AlSi7Mg0 combines aluminum, silicon, and a small amount of magnesium to create a highly durable and lightweight allow suitable for fine objects and complex geometries. It’s used in applications that require a strength/mass ratio as well as good thermal properties.
- Al 6061 & Al 7075. 3D manufacturers are starting to have success with printing using 6061 and 7075, which were previously thought not to be conducive to the AM process. Merging nanoparticles is showing progress.
- Alloys in the 6000 series have properties that make them one of the most popular traditional manufacturing of electrical or electronic parts. They are ductile with high thermal conductivity, electrical conductivity, and corrosion-resistant. 6061 is a precipitation-hardened aluminum allow, containing magnesium and silicon.
- 7000 series alloy powders have a high zinc content, are known for excellent mechanical properties for higher strength and are heat treatable. 7075 is most commonly used in highly-stressed structural parts, such as aircraft parts, and is stronger than many standard structural steels.