Selective laser melting (SLM) is the premier metal 3D printing technology revolutionizing the additive manufacture of metal parts, but how does it work,Learn why!
What Is Metal Sintering?
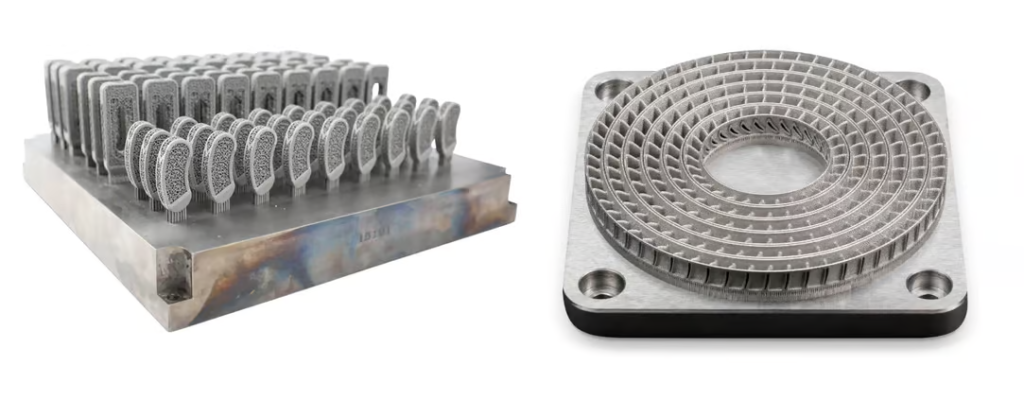
Most metal 3D printers use selective laser melting technology, which involves a laser that melts powdered metal. In fact, this method accounts for more than 80% of the metal 3D printer market.
The dominance of SLM tech may not be apparent at first since there’s different terminology in the industry to refer to the same technology. Aside from SLM, there’s direct metal laser sintering (DMLS), direct metal laser melting (DMLM), laser metal fusion (LMF), laser cusing, and laser powder bed fusion (LPBF),More often today, perhaps because of the various terms and its growing popularity, the technology is commonly referred to simply as metal sintering.
This metal 3D printing, or additive manufacturing, method, is a highly precise technology commonly used for both prototyping and production of end-use, complex metal parts for aerospace, automotive, medical, and industrial applications. It makes everything from tools and spare parts to rocket engines and medical implants.

The reasons behind its rapid growth and adoption are many. First, with an in-house metal 3D printer, companies can produce their own metal parts, such as injection molds, replacement parts, and tools, far faster and cheaper than having them made and shipped from overseas, especially in low volumes. Even ordering parts from a metal sintering service is faster than traditional manufacturing.
Next, metal sintering can produce parts with complex internal channels, lattice-infilled walls, and shapes simply not possible (or prohibitively expensive) with any other manufacturing methods, which leads to better, lighter, and more efficient parts.
Another benefit of metal sintering over traditional manufacturing is sustainability. Especially when printing with high-cost materials, such as titanium or silver. Metal sintering 3D printers use just the material required to build the parts, and the rest can be reused for another part.
How Metal Sintering Works
Like all 3D printing technologies, metal sintering is a digital process that starts with an electronic file of the part. The files is made with computer-aided design (CAD) software or obtained from a digital part repository. Then the design file is put through special build preparation software that breaks it down into slices or layers to be 3D printed. This software, which is often unique to the type of 3D printing and even the brand of 3D printer, generates the path and other instructions for the 3D printer to follow.
Once the part file, which can include dozens of individual parts, is fed to the 3D printer, it prepares to build.
Metal sintering involves a bed of metal powder and high-powered lasers used to selectively fuse metal powder together layer-by-layer on a molecular level until the final part is complete.
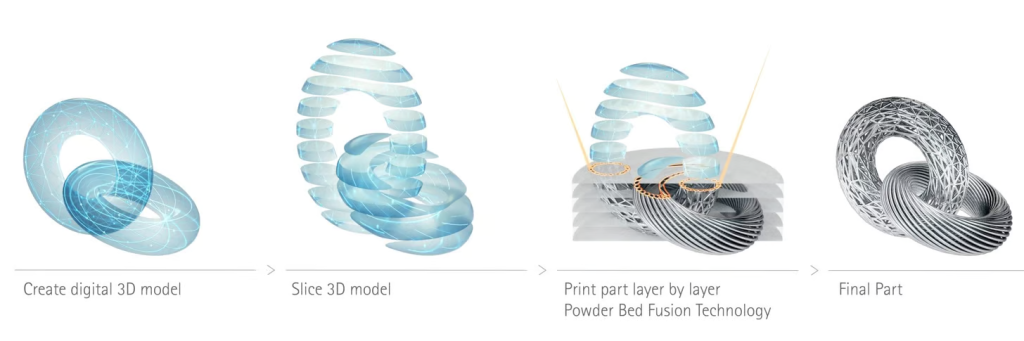
First, the printer hopper is filled with the desired metal powder, then heaters bring the powder to a temperature near the sintering range of the material. The printer pushes powder into the print bed where a recoater blade (like a windshield wiper) or roller spreads it into a thin layer across the build plate. The laser, or lasers, trace the shape of the first layer onto the powder thus solidifying it. The build platform then moves down a tiny amount, and another layer of powder is spread and fused to the first, until the entire object is built. During printing, the build chamber is closed, sealed, and in many cases, filled with inert gas, such as nitrogen or argon blends, which helps prevent debris from the melting process from affecting the part.
The packed powder on the printing bed supports the model during the printing process, but printed supports are also used. The unused metal powder can be mixed with fresh powder and reused for the next print.
After printing, parts are left to cool and the surrounding loose metal powder is removed from the printer. After printing, parts are removed from the powder bed and cleaned. Metal sintered parts can be treated like metal parts produced by conventional metal working for further processing, which may include machining, heat treatment, or surface finishing.
Metal Sintering Advantages & How To Choose
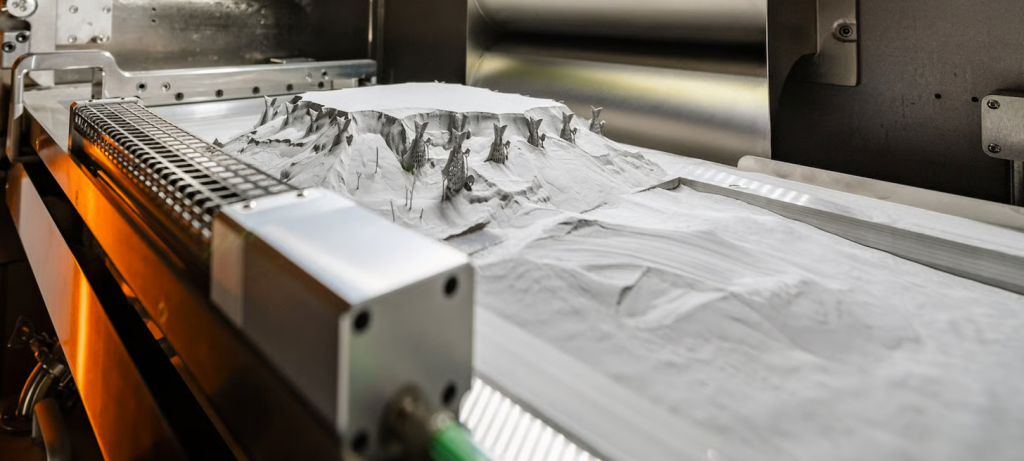
ADVANTAGES
- Extensive range of available metals
- Ability to realize complex shapes or internal structures, possibly without supports
- Reduced total lead times, due to no need for tooling
- Price per part much lower for single pieces or low volumes
- Part consolidation, allowing operators to create previously multi-component parts as one print
- Reduced waste, due to additive manufacturing and powder reclamation
- Ability to reduce standing inventory due to fast on-demand production
- Potential for mass-customization of parts
When selecting a metal sintering 3D printer, consider
- Scalability. If you outgrow the entry-level machine, is there another level to upgrade to?
- Build Speed. How many cubic centimeters per hour can the machine produce?
- Laser Scan Speed. This is not the only indicator in part build speed, but it contributes.
- Laser Spot Size. Can you adjust the laser for more or less detailed parts?
- Layer Height & Resolution. How detailed can the final parts be?
- Gas & Power Consumption. Some machines consume more than others. How does this affect final costs?
- Material Consumption. Machines with good powder feeding and sieving technology can waste less powder.
- Open or Proprietary Materials. If you have to use the printer manufacturer’s materials, it could affect your manufacturing flexibility and costs.
Metals for Metal Sintering
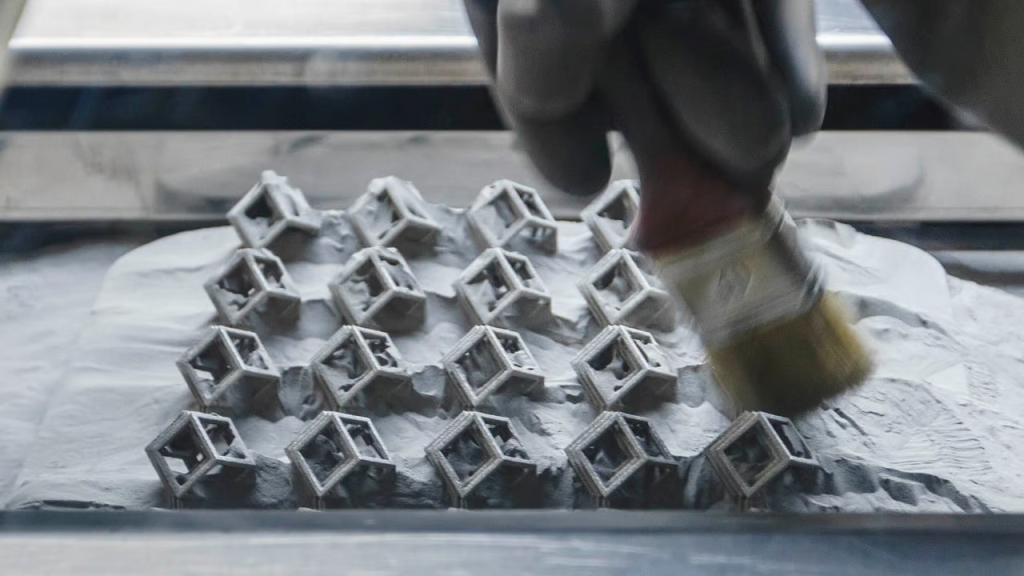
The working material for this 3D printing process is finely powdered metal. Metal powders produced for metal sintering are not the same as metal powders for injection molding. Powders for 3D printing are processed in various ways and differ from each other in their exact chemical makeup, how round the particles are, their density, and more.
Typically the manufactured size of the metal particles is 20 to 40 micrometers. The particle size and shape limit the detail resolution of the final part. Smaller metal particle size and less variation allow better resolution. The characteristics of the raw powder used in a process significantly affect the material properties obtained in the finished component. For this reason, there’s a wide range of material options depending on the application.
There are dozens of metals, including these below, suitable for metal sintering, but not every metal sintering 3D printer can handle the same materials. Some require more powerful lasers or special handling.
Materials for 3D Metal Sintering
- Aluminums
- AlSi10Mg, AlSi7Mg0.6
- Aluminum F357
- Scalmalloy
- Stainless Steels
- 316L
- 15-5PH
- 17-4ph
- 1.2709
- H13
- Invar 36
- 1.4828
- Nickels
- HX
- Inconel 625, 718, 939
- Amperprint 0233 Haynes 282
- Irons
- Titaniums
- Ti6Al4V ELI (Grade 23)
- TA15
- Ti (Grade 2)
- Cobalts
- Coppers
- CuNi2SiCr
- CuCr1Zr
- GRCop-42
- Hastelloy C22, X