Who is 3D printing with titanium today? It’s a broad collection of manufacturers making everything from medical devices, high-performance bicycles, luxury watches, and consumer electronics. What they all have in common is a desire to deliver a lighweight and strong product with innovative, often custom, design.
Precision Products & Electronics
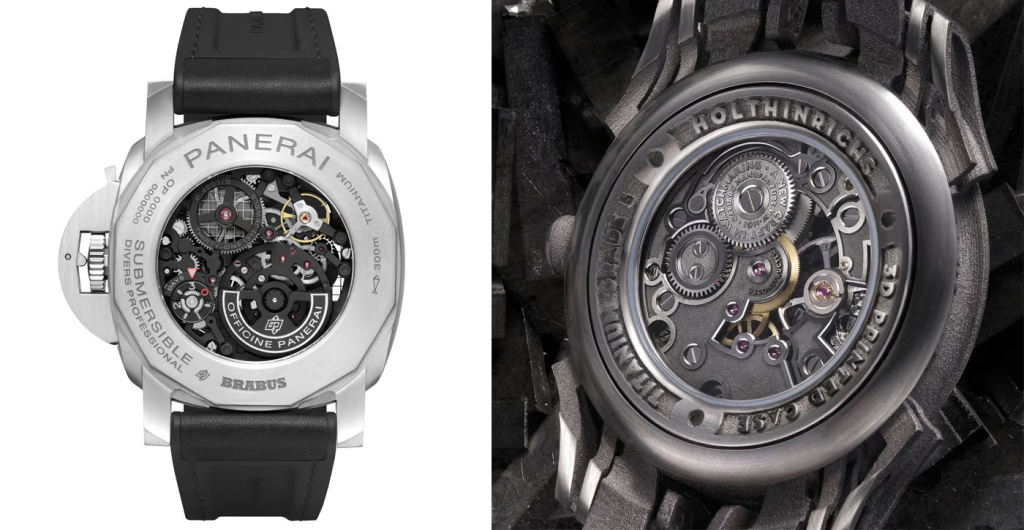
3D printing can create very thin-walled, intricate, and complex titanium parts, which is why it’s used for watch cases, such as the Panerai and Holthinrichs timepieces pictured above and rumored to be an upcoming part of the Apple Watch Ultra.
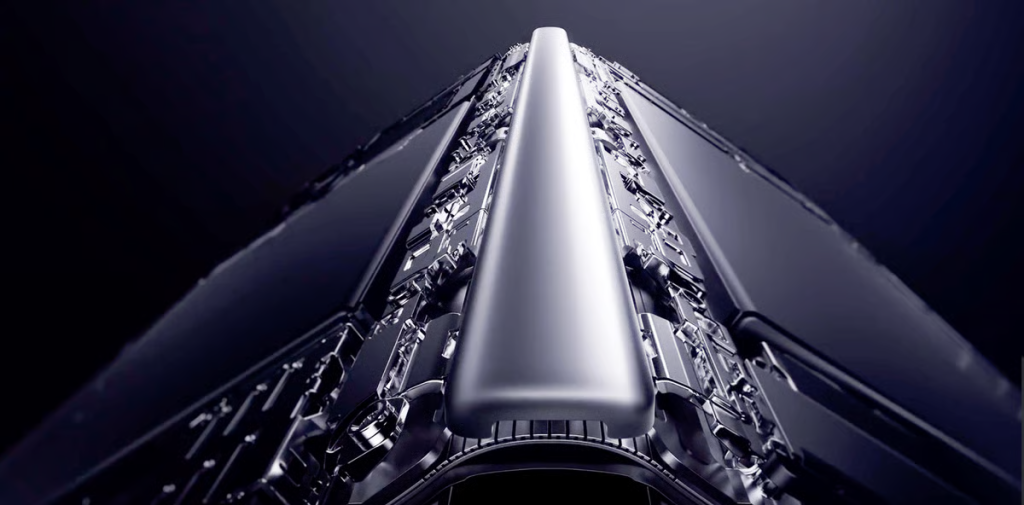
In 2023, smartphone maker Honor introduced the new folding Magic V2 featuring a 3D printed titanium hinge shift cover that’s lighter than the previous aluminum version and 150% stronger. The company says this this small titanium piece, which can be 3D printed in the tens of thousands, is the key to the product’s durable and smooth folding and unfolding.
Medical & Dental Implants

In the medical industry, 3D printed titanium implants are successful across spine, hip, knee, and extremity applications due to the metal’s inherent biocompatibility and good mechanical properties combined with 3D printing’s ability to tailor porous structures — which enable bone integration — and mass customization for better patient outcomes.
3D printed titanium implants are gaining in both regulatory approval and demand. Because most medical implants are manufactured to cover large groups of people with the same condition, they aren’t an ideal fit for everyone. People suffering from rare conditions are often left out. Now, with 3D printing, it is possible to produce implants designed exclusively for individual patients.
Cycling
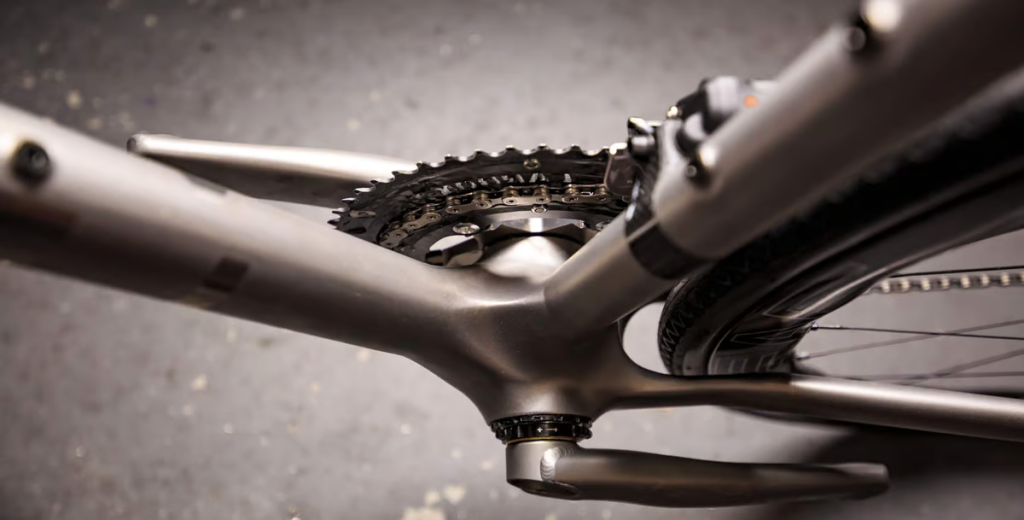
3D printed titanium is almost common in high performance bicycles today where every ounce of weight counts and high-strength is paramount. Used in cranks, break handles, stems, derailleur hangers, and even full frames, titanium is proving as strong as aluminum and as light as carbon fiber, without carbon fibers’ sustainability challenges.
After some prototyping, we found that 3D printed lattice-filled titanium cranks were as light as carbon but more robust in an area that is very exposed to impacts. 3D printed titanium enables it to custom fit bikes to riders’ preferences and the frames do not need any paint or coating.
Aerospace
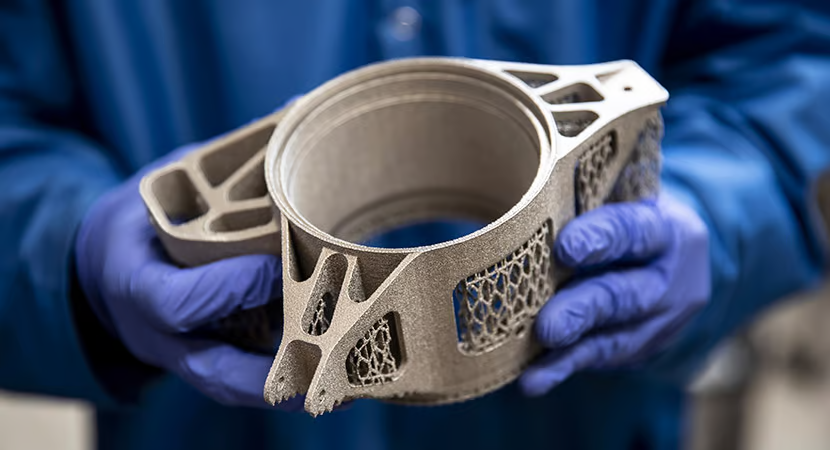
In the aerospace industry, several titanium-based additively manufactured parts are currently in commercial and military use, with numerous other prototypes making their way toward FAA certification. 3D printed titanium is prized for its low “buy-to-fly” ratio — an aerospace term that refers to the correlation between the weight of the initial material and the printed part’s weight.